Improved Deadzones for Continuous 3D Printing
Technology number: 7730
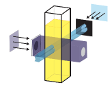
OVERVIEW
Multi-color irradiation for ultra-rapid, continuous 3D printing
- Enables larger dead zones for faster printing without support structures
- Useful for prototyping, industrial manufacturing, medical devices, and customized products
BACKGROUND
The global 3D printing market is currently valued at around $4 billion with forecasted significant growth. Despite its promising potential, 3D printing has lagged behind traditional manufacturing due to high costs, scalability issues, and slower production speeds. A breakthrough called Continuous Liquid Interface Production (CLIP) has improved stereolithographic printing by enabling a continuous printing process, thus increasing speed. However, CLIP technology still faces challenges, particularly in maintaining the “dead zone” that prevents cured resin from sticking to the projection window, which varies with light intensity. High-intensity light speeds up polymerization but reduces the thickness of the “dead zone,” thus limiting the advantages of this technology. To truly capitalize on the benefits of 3D printing, new methods are required to overcome these limitations.
INNOVATION
Researchers have introduced multi-color irradiation to enhance ultra-rapid 3D printing in multiple ways. Instead of using a Teflon film, one wavelength of light creates the dead zone while a different wavelength induces polymerization deeper in the resin bath, making dead zone thickness independent of light intensity. This results in larger dead zones, better resin reflow, and faster continuous printing for larger cross-sectional areas. Additionally, patterned multi-color irradiation allows for 3D patterning to inhibit or initiate polymerization selectively within the resin, eliminating the need for support structures. This is achieved using a novel resin that combines photoinitiators with different absorbance characteristics. The resultant solidified objects possess near-neutral buoyancy, further enhancing printing speed and throughput. Real-world applications include rapid prototyping, industrial manufacturing, medical devices, and customized products, offering transformative advancements in 3D printing capabilities.
ADDITIONAL INFORMATION
INTELLECTUAL PROPERTY:
US12173095B2 "Polymerization photoinhibitor"