One-Step Conversion of Lignocellulosic Biomass to Fumaric and Lactic Acids by Synthetic Fungal Consortia
TECHNOLOGY NUMBER: 7704
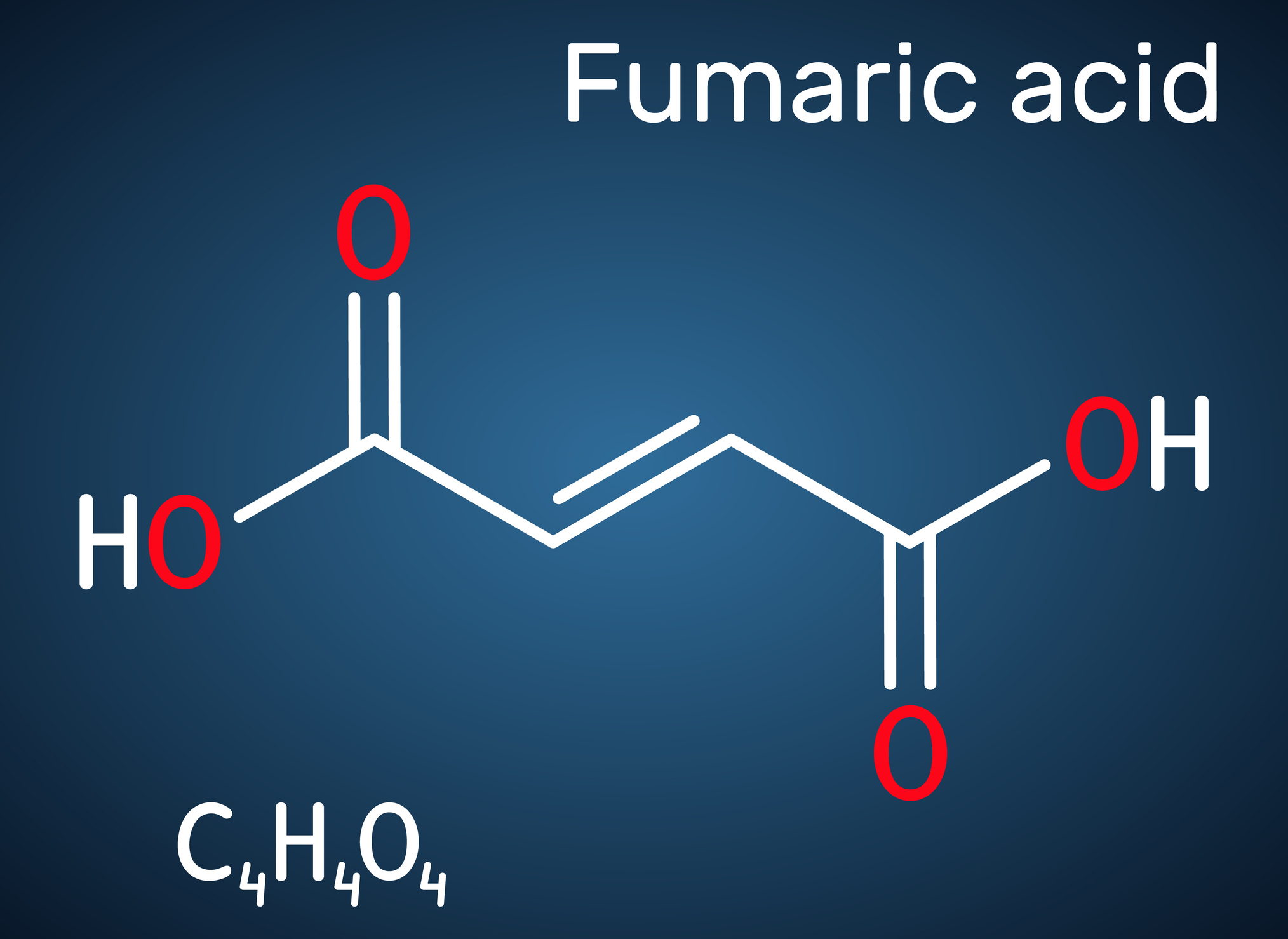
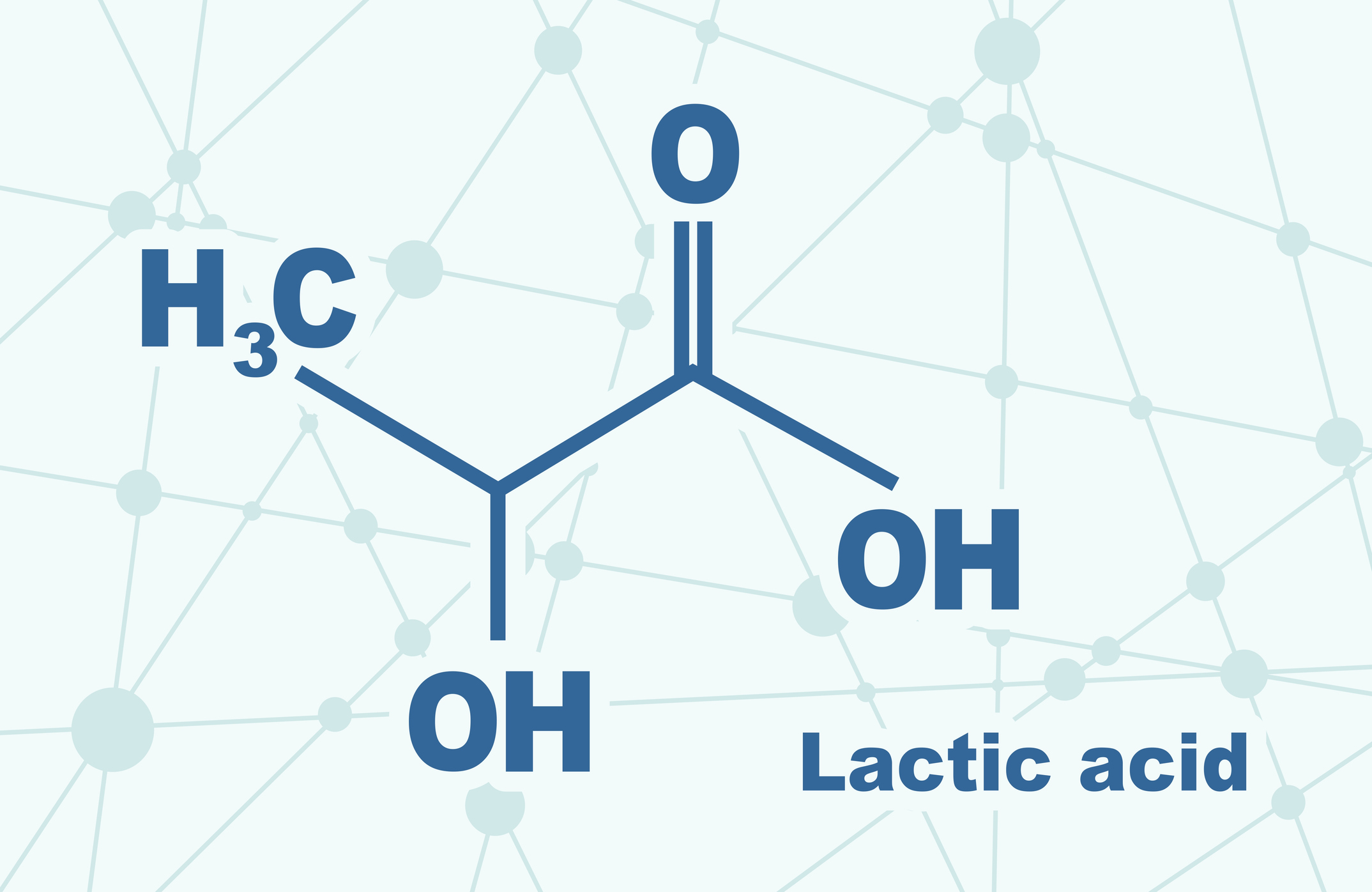
OVERVIEW
One-step conversion of biomass to lactic and fumaric acids using co-cultures.
- Combines all processing steps in one reactor without additional enzymes.
- Biodegradable plastics, food additives, cosmetics, pharmaceuticals, automotive industry materials.
BACKGROUND
Lactic acid and fumaric acid serve numerous industrial applications, ranging from cosmetics and pharmaceuticals to food additives and biodegradable plastics. Lactic acid, in particular, is integral in producing polylactic acid (PLA), an eco-friendly packaging material. The demand for lactic acid is projected to grow substantially, driven to a great degree by the PLA market. Efficient, cost-effective production methods for lactic acid and fumaric acid, especially those utilizing renewable resources, are highly sought after. Traditional methods often involve complex, multi-step processes with high operational costs due to the need for additional enzymes and separate reaction steps. This highlights a significant gap in current production technologies and described the need for a more streamlined, integrated approaches to enhance efficiency and reduce costs.
INNOVATION
Researchers have developed a microbial co-culture that converts lignocellulosic biomass directly into lactic or fumaric acids via consolidated bioprocessing (CBP). This approach integrates cellulase production, cellulose hydrolysis, and fermentation into a single reactor, eliminating the need for external enzyme additions. Unlike previous CBP methods that relied on engineered monocultures, this technology employs a designed co-culture of compatible microorganisms to perform all necessary reaction steps efficiently. This pathway results in significant reductions in processing costs and improved yield and process simplicity. The technology's real-world applications are extensive, including the production of biodegradable plastics like PLA, food and beverage additives, pharmaceutical ingredients, and materials for the automotive industry. These advancements promise more sustainable and economically viable production processes for critical industrial chemicals.