Passive Wireless Strain Sensor
TECHNOLOGY NUMBER: 5829
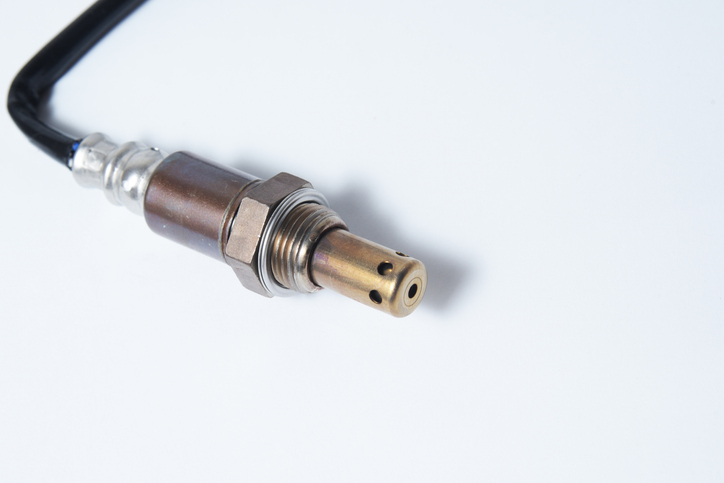
OVERVIEW
Wireless strain sensor with microfabricated magnetoelastic beam element
- Enhances strain sensitivity and range while ensuring passive operation
- Useful for structural health, orthopedic implants, and other strain-sensitive devices
BACKGROUND
Strain sensors play a critical role in monitoring the structural health of various systems, from bridges and buildings to aircraft and medical implants. Historically, strain sensors have relied on electrical resistance or capacitance changes to measure strain, which necessitated complex wiring and power sources. These methodologies often faced limitations such as signal attenuation, orientation dependence, and restricted dynamic range. Additionally, conventional strain sensors required batteries or wired power, complicating their application in inaccessible or moving environments. With the increasing demand for efficient and reliable monitoring technologies in both civil and biomedical fields, there is a pressing need for innovative strain sensing solutions. The development of wireless, passive strain sensors promises to address these challenges by simplifying deployment and maintenance while providing precise and dependable measurements in a variety of conditions.
INNOVATION
Researchers at the University of Michigan have developed a passive, wireless strain sensor leveraging a microfabricated magnetoelastic beam element. This sensor operates based on the ΔE effect of ferromagnetic materials, where mechanical strain induces domain reorientation, altering the material's stiffness. This change is reflected in the resonance frequency, which can be detected wirelessly by an interrogation coil. Fabricated from a 28 μm Metglas™ 2826MB foil using micro-electrodischarge machining, the sensor boasts a notable sensitivity of 1540 ppm/mstrain and a dynamic range of 8 mstrain. The distinctive design includes a spring and resonant strip assembly that mitigates the risk of magnetic saturation, providing flexibility in sensitivity and dynamic range adjustments. Real-world applications include structural health monitoring of infrastructure and in-vivo performance tracking of orthopedic implants, offering enhanced reliability and simplified deployment compared to traditional strain sensors.
ADDITIONAL INFORMATION
US9726557 "Magnetoelastic strain sensor"