Precipitation Printing
TECHNOLOGY NUMBER: 2020-269
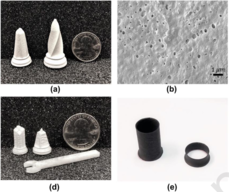
OVERVIEW
An immersion precipitation technology that permits improved control over the porosity of printed parts- Faster printing of a wide variety of polymers with greater porosity control
- Direct additive manufacturing of piezoelectric PVDF without any post-processing
BACKGROUND
Additive manufacturing allows for the fabrication of complex structures which are hard to achieve through conventional machining, extrusion, injection molding or blow molding processes. However, current additive manufacturing methods for polymers still have limitations on the types of polymers that can be 3D printed. A recent innovation in the field is immersion precipitation printing (IPP), which utilizes a solvent reservoir to precipitate the polymer out of the ink. In IPP, a polymer solution is extruded or deposited into a coagulation bath containing a non-solvent, which is miscible with the polymer solvent but does not dissolve the polymer itself. As the polymer solution comes into contact with the non-solvent, the solvent diffuses out, and the polymer precipitates out of the solution, leading to the formation of a solid structure. A need exists for a means to better define the qualities of IPP printed polymers.
INNOVATION
Researchers at the University of Michigan have developed a new immersion precipitation technology that affords greater control over the porosity of the printed parts. Furthermore, they have expanded the approach to polymers that are otherwise difficult to 3D print: poly (vinylidene fluoride) (PVDF), poly (methyl methacrylate) (PMMA), acrylonitrile butadiene rubber (NBR) and multi-walled carbon nanotubes (MWCNTs)-PVDF nanocomposites. Uniquely, the technique prints high beta-phase PVDF that displays piezoelectric behavior without requiring drawing/elongation. The versatility of the technique has been successfully demonstrated by printing a variety of representative structures, ranging from fully functioning 1-way check valves (e.g. artificial hearts), LED pedestal electrodes, and strain gauges. The technology is capable of printing complex geometric shapes with a comparable size and speed of conventional material extrusion approaches. It is also able to print micro-scale structures with greater than 100 micron resolution.