Powered Knee-Ankle Prosthesis with Torque Dense, Low-Ratio Actuation
TECHNOLOGY NUMBER: 2021-177
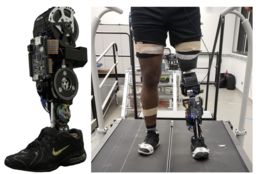
OVERVIEW
A powered knee-ankle leg that implements high torque actuators with low reduction transmissions- Delivers improved functional capabilities while concurrently requiring less energy use
- Combines several factors that permit a more natural gait for post-amputation prosthetic patients
BACKGROUND
The use of conventional passive prostheses after lower-limb loss results in gait that is slower, less stable, and less energy efficient than able-bodied locomotion. Passive prostheses aim to alleviate the effects of amputation using mechanisms such as springs, cams, and dampers to mimic normative gait patterns. However, passive prostheses are limited in functionality due to the fact that such mechanisms can only dissipate energy that the user introduces. Although these passive devices restore some functionality, amputees are typically left with an asymmetric gait. Moreover, most devices are designed for level-ground walking conditions and do not adequately facilitate tasks such as sit-to-stand or stair ascent/descent.
Powered prostheses can actively inject energy and therefore have greater capability to restore mobility and quality of life to those who live with the loss of a limb. A great amount of research has gone into the design and control of powered prosthetic limbs, resulting in several prosthetic devices that implement a variety of actuation schemes. Rigid, or non-backdrivable actuators have recently been implemented in order to reduce the size and weight of the prosthesis, while other prosthetic legs implement actuators with low backdrivability, or high impedance. This approach can cause painful impact forces on the residual limb after extended use, and the requirement for active control of the knee swing results in higher energy consumption and reduced battery life. A need exists for a new prosthetic leg which optimizes functioning and energy use.
INNOVATION
Researchers have developed a powered knee-ankle prosthetic leg that implements high-torque actuators with low-reduction transmissions. The transmission is coupled with a high-torque, low-speed motor to create an actuator with low mechanical impedance and high backdrivability. This style of actuation presents several possible benefits over modern actuation styles in emerging robotic prosthetic legs, which include free-swinging knee motion, compliance with the ground, negligible unmodeled actuator dynamics, less acoustic noise, and power regeneration. A free-swinging knee joint allows for a more natural gait, while reducing the power requirements of the actuator during swing phase. Energy sharing phases of gait such as mid-stance, where the ankle regenerates energy while the knee demands it, can lead to longer periods of untethered operation, which is critical for robotic legs in consumer applications.
Benchtop tests establish that both joints can be backdriven by small torques (~1-3 N-m) and confirm the small, reflected inertia. Impedance control tests prove that the intrinsic impedance and unmodeled dynamics of the actuator are sufficiently small to control joint impedance without torque feedback or lengthy tuning trials. Walking experiments validate performance under the designed loading conditions with minimal tuning. The implementation of biological joint impedances can also promote natural compliance with the ground and provide smoother touchdown impacts, which can in turn improve efficiency of the system and comfort for the user. Finally, the regenerative abilities, low friction, and small reflected inertia of the presented actuators reduced power consumption and acoustic noise compared to state-of-the-art powered legs.