Powered Orthosis with Combined Motor and Gear Technology
TECHNOLOGY NUMBER: 2021-179
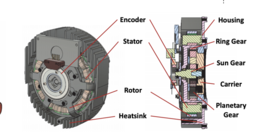
OVERVIEW
A backdrivable powered knee orthosis for partial assistance of lower-limb musculature- Designed for compactness to provide ease of use for patients with arthritis or lower back pain
- Shown in experiments to require less quadricep activation during lifting-lowering, sit-to-stand, and stair climbing
BACKGROUND
Traditional exoskeletons are used to aid paraplegic individuals with little to no voluntary movement, such as may occur after suffering a spinal cord injury or cerebrovascular accident. These orthoses are therefore commonly designed to produce high torque output using highly geared motors to fully support the legs. However, a larger population with musculoskeletal disorders would benefit from partial rather than full assistance of their musculature. Examples of these patient groups include those with osteoarthritis and low back pain, either of which may be contributed to by weak quadriceps musculature. Orthoses that provide assistance in quadricep strength could mitigate arthritis pain by reducing high forces across the knee joint when going from the sitting to standing positions or when walking up stairs. Similarly, quadricep assistance might help relieve back pain from repetitive lifting and lowering tasks. Partial-assist devices must both minimize the torque required by the user to backdrive the actuator during voluntary movements and minimize weight and size for a convenient design. So, a need exists for new partial-assist powered orthoses to improve the lives of patients with these diseases.
INNOVATION
Researchers have invented a novel, backdrivable powered knee orthosis for partial assistance of lower-limb musculature that aims to facilitate daily activities in individuals with musculoskeletal disorders. The actuator design is guided by principles that prioritize compactness, backdrivability, and output torque to permit ease and efficiency of patient movements. This design increases the motor diameter and decreases the transmission ratio while maintaining the desired output torque, thereby reducing the reflected inertia and backdrive torque. Heat output from the device is optimally managed by using a custom brushless DC motor with encapsulated windings. The choice for a 7:1 planetary gearset placed directly into the stator provides the actuator with a package factor that reduces size and weight. Benchtop tests verify that the custom actuator can produce at least 23.9 Nm peak torque and 12.78 Nm continuous torque yet has less than 2.68 Nm backdrive torque during normal walking conditions. Experiments on able-bodied human subjects demonstrate reduced quadriceps activation with orthosis assistance during lifting-lowering, sit-to-stand, and stair climbing. The minimal transmission also produces negligible acoustic noise, permitting patient concentration and communication.